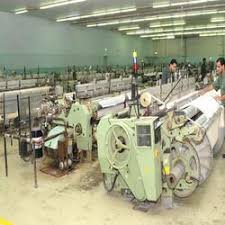
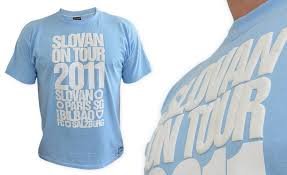
RUBBER PRINTING
- Nov 23rd, 2024
Rubber printing
Rubber printing on fabrics is a popular method used for applying designs, logos, or patterns to textiles, particularly for creating bold, durable prints. This technique involves the use of a rubber-based ink or paste, which is transferred onto the fabric through various printing methods. The rubber print is known for its flexibility, durability, and ability to create vivid, raised designs.
Here’s an overview of the rubber printing process on fabrics:
1. Preparation of the Fabric
- The fabric is typically pre-treated to ensure it is clean, smooth, and ready to accept the printing ink. This may involve washing, heat setting, or applying a base coat.
2. Design Creation
- A design or pattern is created digitally or manually. For rubber printing, designs often include bold colors or textured effects. The design is then transferred to a screen (for screen printing) or stencil (for block printing).
3. Printing Method
There are several methods of rubber printing on fabrics:
- Screen Printing: A stencil (or screen) with the design is placed on the fabric. The rubber-based ink is then forced through the screen, creating the print. This method is ideal for mass production.
- Heat Transfer: A rubber-based design is printed onto a transfer paper, then applied to the fabric using heat and pressure.
- Pad Printing: In this process, a rubber pad is used to pick up the ink and transfer it onto the fabric.
4. Drying and Curing
- After printing, the fabric needs to be dried or cured to set the rubber ink. Curing is usually done with heat, which ensures the ink adheres properly to the fabric and lasts longer without fading or cracking.
5. Post-Treatment
- After curing, the fabric may be washed again, pressed, or treated to ensure the printed design is stable, vibrant, and feels comfortable.
Advantages of Rubber Printing on Fabrics
- Durability: Rubber prints are typically more durable and can withstand repeated washing without significant fading or damage.
- Flexibility: This method is suitable for a wide range of fabric types, including cotton, polyester, and blends.
- Vivid Colors: Rubber-based inks offer excellent opacity and color intensity, which is ideal for bold, eye-catching prints.
- Textured Effects: Rubber printing can create raised or textured designs, which is often used in fashion or sportswear.
Applications
- Clothing: T-shirts, hoodies, sportswear, and other apparel often feature rubber prints for logos, graphics, or brand names.
- Home Décor: Cushions, curtains, and upholstery fabrics may also be rubber printed for custom patterns.
- Advertising: Rubber prints are commonly used in promotional items like bags, hats, and banners.
- Industrial: Some industrial textiles may be rubber printed for added texture or visual design.
Considerations
- Fabric Compatibility: While rubber printing works well on many fabrics, it’s not always suitable for delicate or stretch fabrics.
- Eco-friendliness: Traditional rubber-based inks can be less environmentally friendly compared to other textile printing methods. However, there are newer, eco-friendly rubber ink options available.
- Cost: Rubber printing can be more expensive than other methods like direct-to-garment (DTG) printing, especially for small runs, but it offers a high-quality and long-lasting result.
If you're looking for a service to handle rubber printing on fabrics, it’s important to choose a provider that specializes in this method and offers the kind of quality, durability, and design flexibility you're seeking.